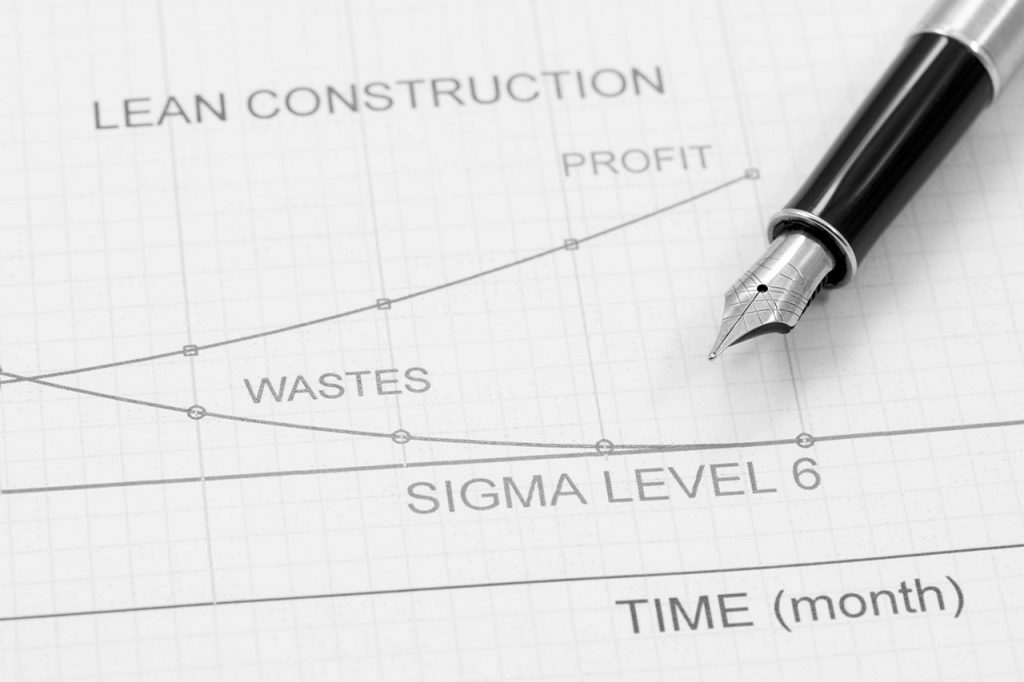
The biggest cost impacting construction today is that of inefficiencies built into the way projects are run and managed – not costs of materials or the cost of labour.
Your project is as strong as your weakest link and as fast as your slowest process.
LEAN Construction is a way to design production systems to minimize waste of materials, time and effort in order to generate the maximum possible amount of value.
Principles of LEAN Construction
- Improving communication
- Eliminating waste and errors
- Direct intervention to drive immediate and apparent change
- Improving work planning and forward scheduling
- Specifying value from the perspective of the customer
- Identifying the processes that deliver customer value (the value stream)
- Eliminating activities that do not add value
- Ensuring the working environment is clean, safe, and efficient
- Continuous improvement

LEAN Construction Techniques
- Using modelling and visualisation techniques to improve planning and communication
- Early planning, to improve workflow, focussing on defining achievable tasks and avoiding mistakes, duplicated effort, out of sequence working and activity that does not add customer value. The objective is the maximisation of workflow and the minimisation of performance variation rather than point speed
- Look-ahead scheduling
- Pre-fabrication and modular building to reduce activity on site and better distribute the workload
- Supply Chain Management and Just-in-time principles
- Benchmarking techniques and the use of key performance indicators
- Critical path analysis and management
- Risk management techniques
Certus Project Solutions can offer guidance and support in the pursuit of LEAN construction in the following areas:
- Project reviews and assessments
- Advanced work package planning
- Last planner system
- Look-ahead schedules and weekly work plans
- Increased vizualization
- Daily work planning
- First run studies
- 5S Process
- Fail safe for quality